In this second installment of our series on the five main technologies for manifold operation and control, we delve into the world of hydraulically operated high-pressure manifolds. While manually operated manifolds are still widely used in today’s oil and gas applications, hydraulically operated manifolds have grown in popularity due to their distinct advantages in terms of safety, power density, and user-friendliness. By leveraging the power of hydraulic fluid, these manifolds offer significant improvements in operational efficiency and manpower reduction compared to their manually operated counterparts.
What is a Hydraulically Operated High-Pressure Manifold?
A hydraulically operated high-pressure manifold utilizes hydraulic power units (HPUs) and hydraulic actuators to automate the operation of plug and choke valves. This setup allows for remote control of the manifold, removing the need for operators to manually adjust valves on-site. This is especially beneficial in high-pressure, high-velocity applications where the manual operation of valves can be both labor-intensive and hazardous.
The basic principle behind hydraulically operated manifolds is simple: by using hydraulic pressure to power the valve actuators, operators can open and close valves remotely, reducing the need for physical intervention at the manifold skid. This technology provides a range of benefits that make it a preferred choice in various industries, particularly in the well stimulating market.
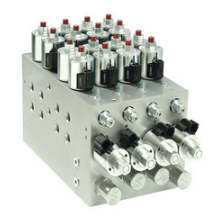
Key Advantages of Hydraulically Operated Manifolds
Hydraulically operated manifolds offer several compelling advantages over manually-operated systems. Below, we’ll explore these benefits in greater detail.
1. High Power Density
One of the most notable advantages of hydraulically operated manifolds is their high-power density. Hydraulic systems are known for their ability to generate immense amounts of force in a compact and lightweight package. This is especially important in applications where space is limited but significant power is required to operate high-pressure valves.
Hydraulic actuators, driven by high-pressure hydraulic fluid, can generate the necessary torque to operate large, heavy-duty valves without requiring bulky, oversized equipment. This high-power density allows for the use of compact actuators that still deliver the performance needed to handle high-pressure fluids in the manifold.
2. User-Friendly Operation
Hydraulically operated manifolds are designed with user-friendliness in mind. Individual valve functions can be controlled using manual handles or push buttons, providing operators with an intuitive interface for operating the system. This simplicity in operation allows for quick and easy adjustments, even in high-stress environments where rapid response times are critical.
By automating the operation of the valves, hydraulically operated manifolds also eliminate the need for manual intervention, reducing the risk of operator error and ensuring more consistent performance.
3. Increased Safety
Safety is a major concern in any industrial operation, and hydraulically operated manifolds provide a significant safety advantage. Unlike manually operated systems that require operators to be physically present at the manifold skid, hydraulically operated systems allow operators to control the valves remotely. This removes the operator from the immediate vicinity of high-pressure and high-velocity fluids, reducing the risk of injury or exposure to hazardous conditions.
Furthermore, the hydraulic control panel or HPU can be located at a safe distance from the manifold, providing an additional layer of protection for the operator. In high-risk environments, this remote operation capability can be a game-changer in terms of ensuring personnel safety.
4. Reliability
Hydraulic systems are known for their reliability. The robust components used in hydraulically operated manifolds, such as hydraulic conductors, pressure intensifiers, and hydraulically piloted directional control valves, are built to withstand the rigors of industrial applications. This durability translates to longer service life, reduced maintenance, and fewer unplanned downtime events.
By relying on proven hydraulic technology, operators can trust that their manifolds will continue to perform even in challenging conditions.
5. Hazardous Certification
Another key benefit of hydraulically operated manifolds is their ability to meet the strict requirements for hazardous area certification. These systems often incorporate low-cost components that are specifically designed for use in hazardous environments. Examples of such components include air-driven pressure intensifiers and hydraulically operated plug and choke valves. This ensures that the system is safe to operate in environments where explosive gases, vapors, or dust may be present.
6. Reduced Operational Costs
Hydraulic automation can also lead to a significant reduction in operational costs. By automating the valve operation process, the need for manual labor is drastically reduced, driving down labor costs. Additionally, the ability to control the valves remotely reduces the likelihood of human error, leading to more efficient operations and fewer costly mistakes.
Potential Drawbacks of Hydraulically Operated Manifolds
While hydraulically operated manifolds offer numerous advantages, they are not without their challenges. Below are some of the potential drawbacks associated with these systems.
1. Operator Mobility
One potential downside of hydraulically operated manifolds is the limitation on operator mobility. Since the HPU and hydraulic control panel are tethered to the manifold via hydraulic hoses, the operator’s range of movement is restricted. While remote operation is possible, the physical connection between the manifold and the control equipment may limit how far away the operator can be positioned.
2. Maintenance Requirements
Hydraulic systems require regular maintenance, particularly when it comes to fluid conditioning and filtration. Hydraulic fluids must be kept clean and free of contaminants to ensure optimal system performance. This requires routine management and may lead to additional operational costs in the form of maintenance labor and replacement parts.
3. Environmental Concerns
Hydraulically operated systems have a higher potential for leaks due to the numerous hydraulic components and connections involved. Fluid leaks not only lead to lost efficiency but also pose environmental risks, especially when hydraulic fluids are not environmentally friendly. These issues can be mitigated through the use of drip pans and environmentally conscious hydraulic fluids, but they still represent a potential challenge for operators.
4. Increased Footprint
Hydraulic equipment, including the control panel, HPU, and fluid conductors, tends to increase the size, space, and weight requirements of the manifold system. This can be problematic in operations where space is limited, and it may necessitate additional planning and resources to accommodate the larger footprint.
5. Longer Startup Time
Another consideration is the additional time required to connect the manifold with the remote hydraulic control panel, HPU, and numerous hoses during system startup. This can add to the overall setup time for the system, potentially delaying operations in time-sensitive environments.
6. Higher Installed Costs
The capital investment required for a hydraulically operated manifold system is generally higher than that for manually-operated systems. This is due to the additional equipment required, such as the HPU, control panel, and hydraulic actuators, as well as the ongoing maintenance and operational costs associated with maintaining the system.
Conclusion
Despite some drawbacks, hydraulically operated high-pressure manifolds remain a field-proven technology that offers reliability, safety, and efficiency in manifold operation. The high-power density and user-friendly operation make them an attractive option for industries such as oil and gas, where automation and remote operation are key to improving safety and reducing labor costs.
While the additional hydraulic equipment may increase the system’s footprint and installation costs, the enhanced safety, ease of operation, and long-term reliability more than justify the investment for many operators. For well stimulation and other applications that require precise control of high-pressure valves, hydraulically operated manifolds are a smart and effective solution.
Stay tuned for the next blog in our series, where we’ll cover the three remaining operating technologies: pneumatic, electric, and wireless manifolds.